Global logistics is a dirty business. Emissions from shipping are up 90% since 1990. Today we emit over one billion tons of CO2 every year to ship goods around the world. “If the international shipping sector were a country, it would be the sixth largest emitting nation in the world.”
We should recognize that about 40% of those emissions are going into transporting fossil fuels around the world on ships loaded up with coal, gas, and oil. So in a world that no longer burns carbon for energy we can take that 40% right off the top.
Shipping has long been considered one of the hardest to abate sectors of our economy as it relies almost entirely on the use of fossil fuels to move very heavy trucks, cargo ships, and trains. Methods of decarbonization tend to look at finding efficiencies on the margins like making containers lighter by making them out of plastic. Many of these ideas seem narrowly focused (e.g. what about all that plastic?) and do not take a whole systems perspective.
But thinking about shipping containers might actually make sense. Because if we were to step all the way back and design a pathway to a zero emissions global supply chain, what better place to start than with the one thing that unites three modes of transportation together—the intermodal freight container!
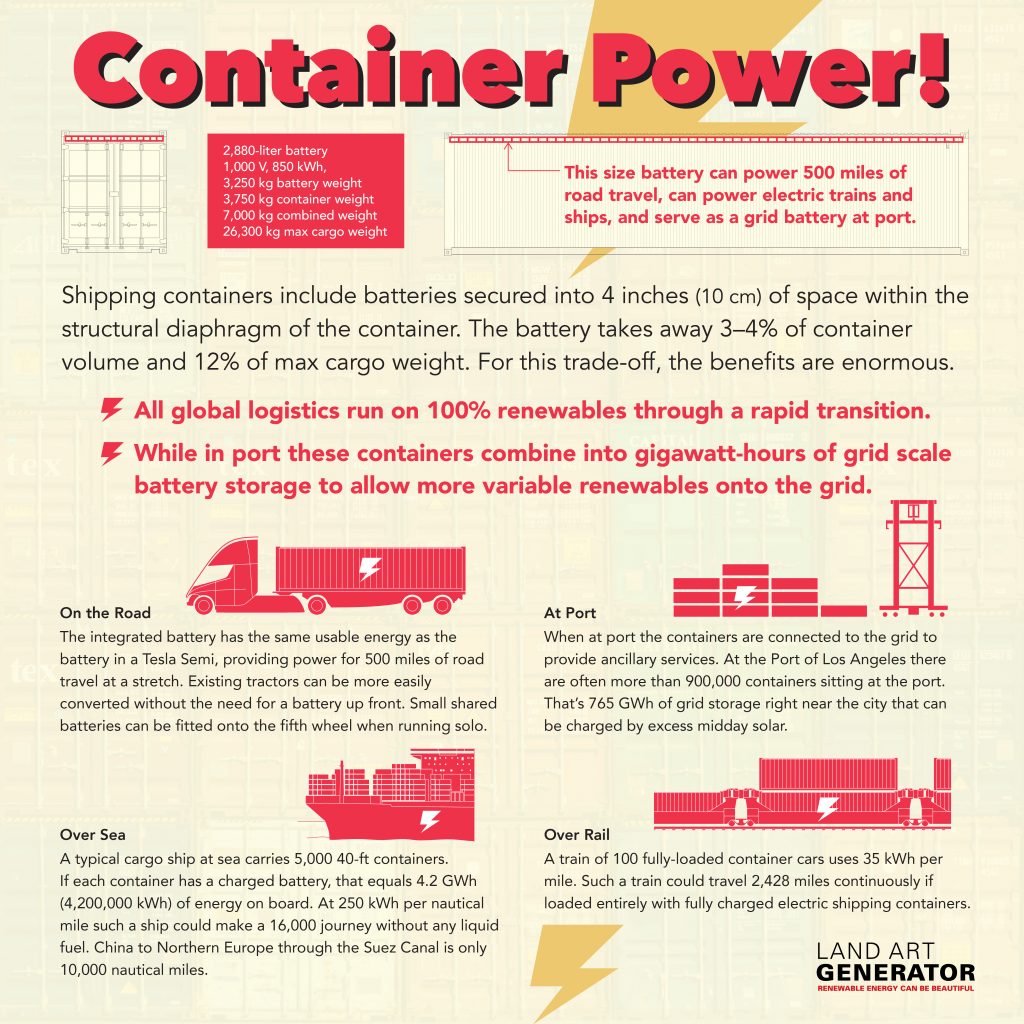
This standardized reusable metal box is an invention that already made logistics orders of magnitude more efficient. Perhaps it still has some tricks up its sleeve.
According to Wikipedia there are “about seventeen million intermodal containers in the world, and a large proportion of the world’s long-distance freight generated by international trade is transported in shipping containers.”
Reusable steel truck-sized shipping containers first came into use in the late 1950s following the U.S. military’s experiments with standardization of shipping units for efficiency. While there are many who were involved in those efforts, we really have Malcolm McLean to thank for the version we are all familiar with today.
American entrepreneur Malcolm McLean realized that by standardizing the size of the containers being used in global trade, loading and unloading of ships and trains could be at least partially mechanized, thereby making the transfer from one mode of transportation to another seamless. This way products could remain in their containers from the point of manufacture to delivery, resulting in reduced costs in terms of labor and potential damage.
In 1956 McLean created the standard cargo container, which is basically still the standard today. He originally built it at a length of 33 feet – soon increased to 35 – and 8 feet wide and tall.
This system dramatically reduced the cost of loading and unloading a ship. In 1956, manually loading a ship cost $5.86 per ton; the standardized container cut that cost to just 16 cents a ton. Containers also made it much easier to protect cargo from the elements or thieves, since they are made of durable steel and remain locked during transport.
What if we could integrate the power needed to move goods around the world right into the very box that moves them? Malcolm McLean might have loved the idea.
There has been a lot of research and development on electrifying all of the various modes of transport, like finding a way to fit enough batteries under the seat of a semi truck to be able to pull a 40-foot trailer loaded with stuff for 500 miles on a highway. Electrifying container ships is an even tougher challenge.
If we were to take those same batteries from under the seat and instead place them in every container, then the power goes exactly where it’s needed, regardless of the mode of transport. And the modes of transport are just electric motors waiting to plug into the power from the container. The race toward electrified trucking no longer needs to worry about battery space and can move on to new challenges.
A universal power interface would be built into the container connecting the battery in the container to a receptacle built into the trailer of the truck, into the hull of the ship, and into the bed of the train car.
As an added bonus of this new global logistics system, the containers would also plug in at the port. There—as they wait to be boarded onto a ship or onto a train—they would be connected to the entire energy grid. When grid operators need power they know they have a reserve to rely on. The scale of this grid service component could be massive.
At the Port of Los Angeles there are often more than 900,000 containers sitting at the port. That’s 765 GWh of grid storage right near the city that can be charged by midday excess solar and send that electricity back to the grid.
As of 2024 the entire battery energy storage system of the State of California was 40 GWh. Imagine multiplying that by twenty. There would be absolutely no need for gas peaker plants. We could build as much variable renewables as data centers demand of us. Of course we’d need to ensure the electricity distribution infrastructure could handle it, but the great thing about this is that the power storage is basically located in the heart of the demand center. The Port of Los Angeles is exactly next to where all the power demand is coming from. No long-distance transmission required!
The real value of the load balancing services that these containers plugged in at port would provide is massive. Financing with this future income in mind could be the tool that makes such an ambitious transition possible.
Companies have a lot to gain from decarbonizing their supply chains. Shipping is the largest component of Scope 3 emissions and so financing for this transition would be heavily supported by advance market commitments that can support their Scope 3 reduction accounting.
The process of conversion from standard container to power container could happen gradually as the supporting infrastructure is put in place on trains, trailers, ships, and ports. Existing containers in decent shape would be retrofitted with batteries and the supporting hardware to interface with transportation modes and the grid. Nearly all new shipping containers would come built with the batteries integrated already, across all the different types available.
One of the potential concerns is the vandalism and neglect that shipping containers are famous for enduring. Adding additional value to containers, making them objects of greater worth, can actually help to address the issue that many of them end up discarded with it costs more to return them to their port of origin. If they house useful energy storage technology, then they will be more highly valued and cover their own cost of return travel.
As far as theft is concerned, is easy enough to make the housing tamper resistant. If we can do this with a million street scooters then we can do this with containers. Other types of tractor-trailer combinations that are not hauling intermodal containers would still need batteries in the tractor unit, but for some routes we could even provide catenary systems to limit the size of battery requirements.
There may be other reasons this is not a good idea. The battery weight is the most challenging part. In fact the way the battery is shown in the information graphic is best for efficiency of fitting goods into the container, but it would probably make the container too top-heavy, especially in the context of road freight negotiating winding mountain passes. Perhaps the battery could be built into the sides of the container. Or it could sit in the back, but this would make the container unbalanced. It could even be built into a strong floor, but this would create other challenges along with probably more weight.
In any event, if we are serious about meeting our climate obligations, then we should be looking deeply at every possible solution, especially those that offer a system scale pathway.
It is also important to remember that, while the system we developed since the 1950’s seems immutable, like it just is the way it is,in fact it is not really that old and we should feel the freedom to redesign it entirely from first principles. This is especially true since in the 1950’s the concept of global heating was not yet widely understood. If Malcolm McLean and his contemporaries had known about climate change, how would they have imagined the idea of shipping containers?
On the Road
The integrated battery is the same size as the battery in a Tesla Semi, providing power for 500 miles of road travel at a stretch. Existing tractors can be more easily converted without the need for a battery in the chassis—just the motor. Small shared batteries can be fitted onto the fifth wheel when running solo.
Over Sea
A typical cargo ship at sea carries 5,000 40-ft containers. If each container has a charged battery, that equals 4.2 GWh (4,200,000 kWh) of energy on board. At 250 kWh per nautical mile such a ship could make a 16,000 journey without any liquid fuel. China to Northern Europe through the Suez Canal is only 10,000 nautical miles.
Over Rail
A train of 100 fully-loaded container cars uses 35 kWh per mile. Such a train could travel 2,428 miles continuously if loaded entirely with fully charged electric shipping containers.
At Port
When at port the containers are connected to the grid to provide ancillary services. At the Port of Los Angeles there are often more than 900,000 containers sitting at the port. That’s 765 GWh of grid storage right near the city that can be charged by excess midday solar.